Now that we've looked at some of the general principles of tunnel building, let's consider an ongoing tunnel project that continues to make headlines, both for its potential and for its problems. The Central Artery is a major highway system running through the heart of downtown Boston, and the project that bears its name is considered by many to be one of the most complex -- and expensive -- engineering feats in American history. The "Big Dig" is actually several different projects in one, including a brand-new bridge and several tunnels. One key tunnel, completed in 1995, is the Ted Williams Tunnel. It dives below the Boston Harbor to take Interstate 90 traffic from South Boston to Logan Airport. Another key tunnel is located below the Fort Point Channel, a narrow body of water used long ago by the British as a toll collection point for ships.
Before we look at some of the techniques used in the construction of these Big Dig tunnels, let's review why Boston officials decided to undertake such a massive civil-engineering project in the first place. The biggest issue was the city's nightmarish traffic. Some studies indicated that, by 2010, Boston's rush hour could last almost 16 hours a day, with dire consequences both for commerce and quality of life for residents. Clearly, something had to be done to relieve traffic congestion and make it easier for commuters to navigate the city. In 1990, Congress allocated $755 million to the massive highway improvement project, and a year later, the Federal Highway Administration gave its approval to move ahead.
The Big Dig kicked off in 1991 with construction of the Ted Williams Tunnel. This underwater tunnel took advantage of tried-and-true tunneling techniques used on many different tunnels all over the world. Because the Boston Harbor is fairly deep, engineers used the cut-and-cover method. Steel tubes, 40 feet in diameter and 300 feet long, were towed to Boston after workers made them in Baltimore. There, workers finished each tube with supports for the road, enclosures for the air-handling passages and utilities and a complete lining. Other laborers dredged a trench on the harbor floor. Then, they floated the tubes to the site, filled them with water and lowered them into the trench. Once anchored, a pump removed the water and workers connected the tubes to the adjoining sections.
The Ted Williams Tunnel officially opened in 1995 -- one of the few aspects of the Big Dig completed on time and within the proposed budget. By 2010, it is expected to carry about 98,000 vehicles a day.
A few miles west, Interstate 90 enters another tunnel that carries the highway below South Boston. Just before the I-90/I-93 interchange, the tunnel encounters the Fort Point Channel, a 400-foot-wide body of water that provided some of the biggest challenges of the Big Dig. Engineers couldn't use the same steel-tube approach they employed on the Ted Williams Tunnel because there wasn't enough room to float the long steel sections under bridges at Summer Street, Congress Street and Northern Avenue. Eventually, they decided to abandon the steel-tube concept altogether and go with concrete tunnel sections, the first use of this technique in the United States.
The problem was fabricating the concrete sections in a way that allowed workers to move into position in the channel. To solve the problem, workers first built an enormous dry dock on the South Boston side of the channel. Known as the casting basin, the dry dock measured 1,000 feet long, 300 feet wide and 60 feet deep -- big enough to construct the six concrete sections that would make up the tunnel. The longest of the six tunnel sections was 414 feet long, the widest 174 feet wide. All were about 27 feet high. The heaviest weighed more than 50,000 tons.
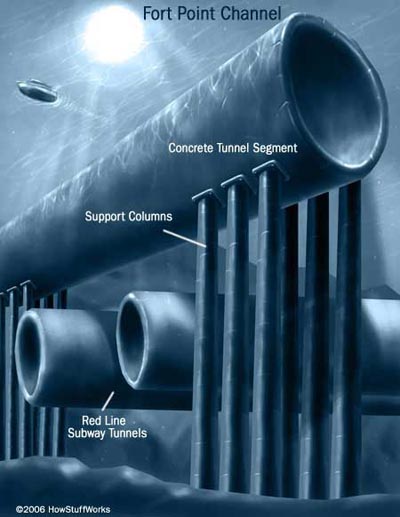
|
The completed sections were sealed watertight at either end. Then workers flooded the basin so they could float out the sections and position them over a trench dredged on the bottom of the channel. Unfortunately, another challenge prevented engineers from simply lowering the concrete sections into the trench. That challenge was the Massachusetts Bay Transportation Authority's Red Line subway tunnel, which runs just under the trench. The weight of the massive concrete sections would damage the older subway tunnel if nothing were done to protect it. So engineers decided to prop up the tunnel sections using 110 columns sunk into the bedrock. The columns distribute the weight of the tunnel and protect the Red Line subway, which continues to carry 1,000 passengers a day.
The Big Dig features other tunneling innovations, as well. For one portion of the tunnel running beneath a railroad yard and bridge, engineers settled on tunnel-jacking, a technique normally used to install underground pipes. Tunnel-jacking involves forcing a huge concrete box through the dirt. The top and bottom of the box support the soil while the earth inside the box was removed. Once it was empty, hydraulic jacks pushed the box against a concrete wall until the entire thing slid forward five feet. Workers then installed spacer tubes in the newly-created gap. By repeating this process over and over, engineers were able to advance the tunnel without disturbing the structures at the surface.
Today, 98 percent of the construction associated with the Big Dig is complete, and the cost is well over $14 billion. But the payoff for Boston commuters should be worth the investment. The old elevated Central Artery had just six lanes and was designed to carry 75,000 vehicles a day. The new underground expressway has eight to ten lanes and will carry about 245,000 vehicles a day by 2010. The result is a normal urban rush hour lasting a couple of hours in the morning and evening.
To see how the Big Dig compares to other tunnel projects, see the table below.
Tunnel |
Location |
Length |
Years to Build |
Opened |
Cost |
Railway Tunnels |
Seikan Tunnel |
Japan |
33.5 mi (53.9 km) |
24 |
1988 |
$7 billion |
Channel Tunnel |
England-France |
30.6 mi (49.2 km) |
7 |
1994 |
$21 billion |
Apennine Tunnel |
Italy |
11.5 mi (18.5 km) |
14 |
1934 |
|
Hoosac Tunnel |
United States |
4.75 mi (7.6 km) |
22 |
1873 |
$21 million |
Motor-Traffic Tunnels |
Laerdal Tunnel |
Norway |
15.2 mi (24.5 km) |
5 |
2000 |
$125 million |
St. Gotthard Road Tunnel |
Switzerland |
10.1 mi (16.2 km) |
11 |
1980 |
|
Bridge-Tunnel Complexes |
Chesapeake Bay Bridge-tunnel |
United States |
17.6 mi (28.3 km) |
3.5 |
1964 |
$200 million |
Øresund Bridge and Tunnel |
Denmark-Sweden |
9.9 mi (16 km) |
8 |
2000 |
$3 billion |
The Future of Tunneling
As their tools improve, engineers continue to build longer and bigger tunnels. Recently, advanced imaging technology has been available to scan the inside of the earth by computing how sound waves travel through the ground. This new tool provides an accurate snapshot of a tunnel's potential environment, showing rock and soil types, as well as geologic anomalies such as faults and fissures.
While such technology promises to improve tunnel planning, other advances will expedite excavation and ground support. The next generation of tunnel-boring machines will be able to cut 1,600 tons of muck per hour. Engineers are also experimenting with other rock-cutting methods that take advantage of high-pressure water jets, lasers or ultrasonics. And chemical engineers are working on new types of concrete that harden faster because they use resins and other polymers instead of cement.
With new technologies and techniques, tunnels that seemed impossible even 10 years ago suddenly seem doable. One such tunnel is a proposed Transatlantic Tunnel connecting New York with London. The 3,100-mile-long tunnel would house a magnetically-levitated train traveling 5,000 miles per hour. The estimated trip time is 54 minutes -- almost seven hours shorter than an average transatlantic flight.
For lots more information about tunnels and related topics, check out the links on the next page.